Volunteer corn (corn growing due to seed from the previous year’s crop) can be a serious problem, and according to a 2007 Iowa State University study one volunteer corn plant per 10-foot of row resulted in a 1.3 percent yield loss. I haven’t seen many fields worst than this one…
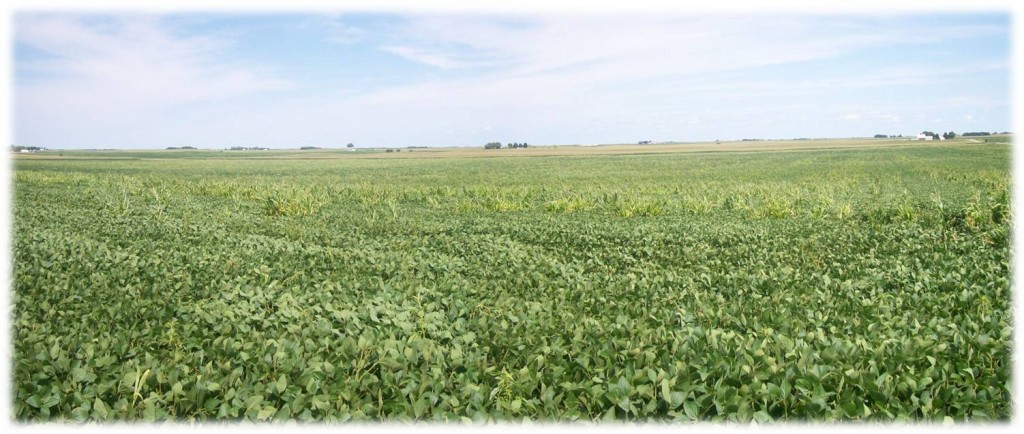
Got Volunteer Corn?
Algona, Iowa – Corn is so important in Iowa that the Algona municipal airport’s runway is bordered by it! I guess every piece of arable land is being used!
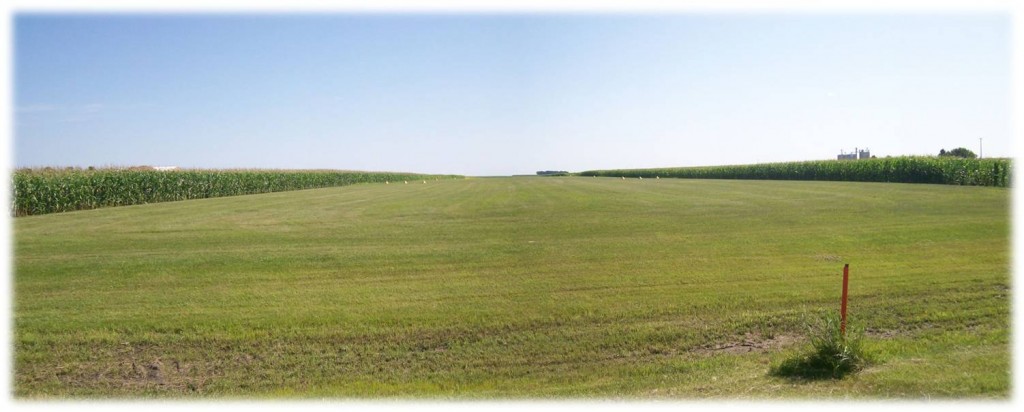
Algona, Iowa - Municipal Airport Runway
(Okay, so to be entirely truthful – Algona does have a paved runway — so this is not the only runway at the airport.)
Britt, Iowa — National Hobo Convention
Yes, you read it correctly! Britt, Iowa is home to the national hobo convention, which is being held this summer from August 6-9. For more information and to find out who a hobo really is check out their website: Britt, Iowa.
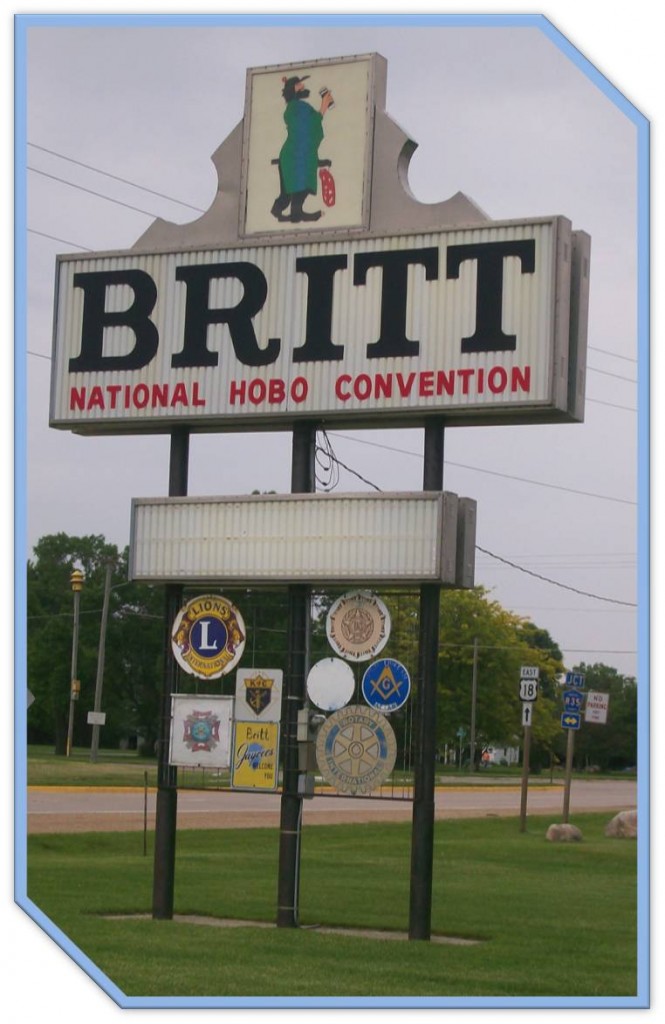
Britt, Iowa