By Barry Putnam and Mary Kate MacKenzie
Lean Management is a systematic approach to analyze and continuously improve the flow of information, materials, and work in a manufacturing environment. Lean systems maximize production efficiency by minimizing waste and disruptions. Lean principles and practices emerged from the Japanese auto manufacturing industry in the 1950s, and managers have since applied them across many other industries, including agriculture. As farm managers strive to utilize labor and other inputs more efficiently in response to rising costs, Lean Management offers a promising tool.
When trying to understand what Lean is, it can be helpful to think about what Lean is not. Disorganized procedures that waste time and materials, frustrate employees, or cause disruptions in production activities are definitely not Lean. How much time do managers on your farm spend responding to crises and putting out fires versus setting up systems that eliminate the root cause of those problems? How often does a ten-minute task take twenty minutes or more because the right tools and materials are not immediately available? How often does a failure to communicate critical information cause a quality defect or production delay? Lean Management invites farm operators to shift away from a reactive problem-solving mindset toward proactive process design grounded in continuous improvement.
In the spring of 2021, the Pro-Dairy Farm Business Management team identified Lean Management as an opportunity to help dairy operators measure and improve performance. We developed a Lean Activity Project to teach farm managers about Lean principles and practices, and we asked each participant to implement a Lean process improvement. Our team created educational materials that guided farm managers through selecting and observing a production activity, measuring waste, designing and implementing a change, and evaluating the impact. We shared project materials with 120 farms and provided additional support through three webinars and individual consultations.
Dairy operators have been seeking efficiency gains for many years, so Lean principles and practices are not entirely foreign. Most farms engaged in the Lean Activity Project had examples of past projects that demonstrated Lean concepts. However, most of these examples were motivated by a specific problem. Few farms reported using Lean Management proactively to identify waste and improve business processes.
About a quarter of farms engaged in the Lean Activity Project completed a Lean process improvement during the summer 2021 project timeline. Their projects addressed a wide range of production activities across different business areas. Several farms focused on the shop, developing Lean processes for inventorying shop parts and performing equipment maintenance. One farm cut twelve minutes off skid steer preventative maintenance by purchasing a rolling cart and assembling all the necessary tools and supplies on the cart before starting to work on the skid steer. Employees can use the same cart to assemble parts and supplies for other maintenance tasks, further reducing wasted steps in the shop.
Other Lean shop projects addressed flows of information. One farm developed a new procedure for assembling shopping lists to streamline purchasing. Another standardized their process for recording and tracking vehicle maintenance. A third farm piloted the use of smartphone apps to create to-do lists, assign tasks, and improve communication among shop employees. These process improvements will help farms stay on top of preventative maintenance and make shop employees more productive, while reducing delays caused by supply shortages and equipment breakdowns.
Farms also implemented process improvements related to livestock handling and management. One dairy set up a gate repair kit in each barn, and implemented a procedure for inventorying and restocking supplies in all the kits. This change saved time on gate repair, and reduced the risk of cows getting into the wrong group due to broken gates. Another farm set up a new storage area for medications in the calf barn, eliminating unnecessary steps taken by employees who manage and treat calves.
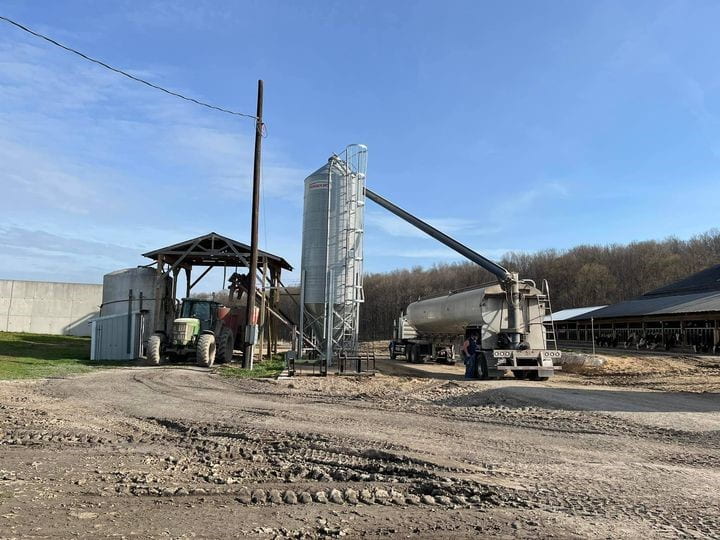
Some of the largest efficiency gains documented by participating farms came from changes to the layout of the feed center or the fuel center. One dairy previously experienced feeding delays on a weekly basis when delivery trucks blocked access to feed bins. After moving feed bin augers to the opposite side of the feed center, an employee can now load the wagon while delivery trucks unload, eliminating waiting and disruptions to the feeding schedule. Another dairy set up an old fuel tank next to the feed center, and transported diesel from their fuel center to their feed center using an existing fuel truck. As a result, equipment used at the feed center now gets fuel at the feed center, eliminating 6.5 trips per day, on average, down a bumpy driveway to the fueling center and back. The farm estimates this change will save 657 hired labor hours per year.
Dairy production systems are complex, offering endless opportunities to streamline and improve procedures. Our project examples demonstrate that farm managers can achieve measurable results by implementing low-cost changes in a relatively short timeframe. One change often leads to another, as farms that successfully implemented one Lean improvement came away with ideas for more. Several participating farms also reported positive impacts on employee morale. Employees responded well to process changes when managers included them in the planning process and incorporated their ideas, and when the changes made their jobs easier.
One of the biggest challenges that dairy operators reported was deciding where to start. With so many possible places in which to deploy Lean Management, it can be overwhelming to select just one. Dr. Abbot Maginnis, Director of the Lean Graduate Certificate Program at the University of Kentucky, recommended during a presentation at the 2022 Northeast Dairy Management Conference selecting one model area within the business to begin implementing Lean improvements. By restricting the scope of Lean Management to one area of the business, managers and employees can learn to develop and sustain Lean systems in a limited way, building skills and confidence before spreading the approach to other areas of the business. Starting small can also help farm managers gain buy-in from employees before tackling larger projects.
It is easier than most people think to get started with Lean Management. The keys to success include starting small and engaging frontline workers. With practice, operators can shift away from a reactive, problem-solving mindset toward a more proactive approach to identifying and reducing waste. Dairy operators often think about managing assets, yet they also manage processes. Lean challenges operators to adopt a process centric lens. Change takes time and requires discipline, commitment and practice. However, to quote Clarence W. Barron, grandfather of financial reporting, “everything can be improved.”
This article appeared in PRO-DAIRY’s The Manager published by Progressive Dairy. To learn more about Cornell University CALS PRO-DAIRY, visit prodairy.cals.cornell.edu.